Но увеличивать одну только подачу топлива бесполезно – без кислорода оно не будет сгорать полностью. Поэтому, чтобы поднять мощность, нужно либо увеличивать объем цилиндров, либо – подавать в тот же объем больше воздуха, в котором сможет сгорать больше топлива.
Такие системы начинают появляться на автомобилях с конца 20-х – начала 30-х годов ХХ века, и сегодня в серийном производстве – несколько разновидностей конструкций наддува. Это прежде всего механический компрессор, состоящий из вращающегося ротора с лопатками, приводимого в действие ременной передачей от двигателя либо отдельным электромотором. Интересной конструкцией выступает волновой нагнетатель, когда ротор имеет аксиально расположенные камеры-ячейки, проходя через которые выхлопные газы создают разряжение, за счет чего всасывается воздух. Не вполне типичен спиральный или G-образный наддув, состоящий из двух спиралевидных частей – неподвижной внешней (корпус) и подвижной внутренней (вытеснитель), которая, вращаясь, совершает колебательные движения, отчего образуются серпообразные полости, они движутся к центру, перемещая воздух в двигатель.
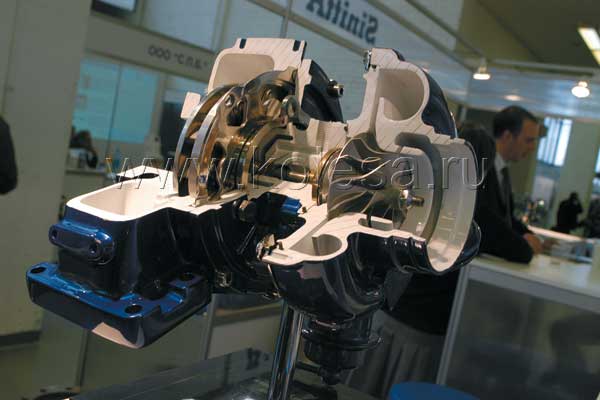
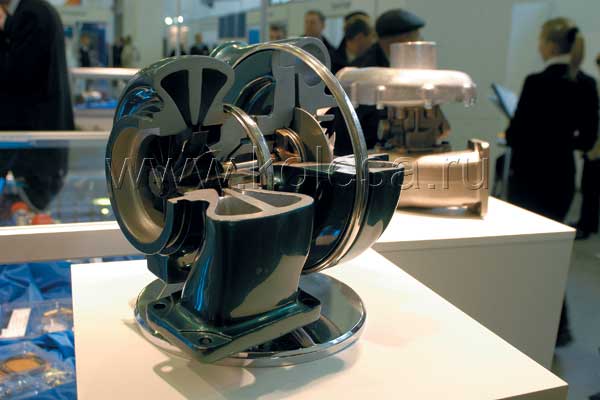
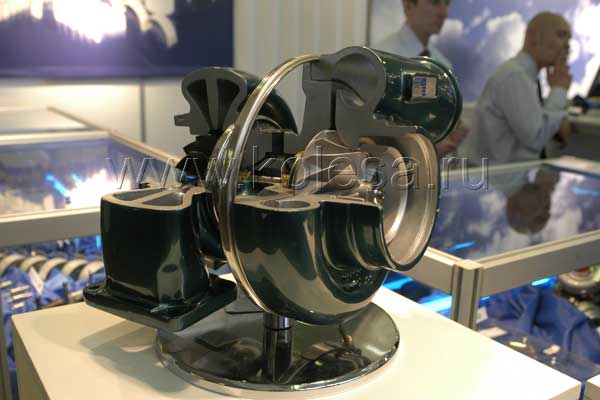
Но наибольшее распространение получил на сегодня турбонаддув – компрессор с приводом от турбины, которым сейчас оснащается большинство дизелей и целый ряд бензиновых моторов.
Усилитель
Принципиальная схема устройства турбокомпрессора достаточно проста. Он состоит из установленных на общем валу и заключенных в единый корпус двух турбин – роторов с лопатками, один вращается потоком выхлопных газов и соответственно вращает другой, который нагнетает воздух в цилиндры. Однако технически при этом приходится решать целый ряд проблем, что делает турбокомпрессор достаточно инженерносложным и дорогим узлом.
В первую очередь, это проблема инерции турбины, которой при повышении оборотов еще нужно некоторое время, чтобы раскрутиться. Отсюда и возникает тот известный эффект "турбоямы", когда на резкое нажатие газа двигатель откликается не сразу – сначала "думает", а потом вдруг резко "подхватывает". Инерционность влечет и другую крайность: раскручиваясь, на высоких оборотах турбина начинает нагнетать воздух под чрезмерным давлением. И наоборот – при низких оборотах, когда поток выхлопных газов невелик, она крутится слабо.
Наиболее распространенным в автостроении решением выступает система управления давлением наддува, в которой часть выхлопных газов может перепускаться мимо турбины. Таким образом, на высоких оборотах сбрасывается излишнее давление, а на низких, напротив, создается максимальное и весь поток направляется на турбину, которая начинает раскручиваться быстрей, что позволяет уменьшить "турбояму". Технически это реализуется посредством тарельчатых клапанов или поворотной заслонки, величиной открытия которых через сервопривод управляет электронный блок.
Для полной ликвидации "турбоямы" и повышения момента на низких оборотах у некоторых "продвинутых" моторов в дополнение к турбокомпрессору устанавливается механический, который, имея практически мгновенный "отклик", закрывает инерционные провалы турбины. Кроме этого, весьма перспективной в настоящее время выглядит конструкция турбины с изменяемой геометрией, имеющей управляемые поворотные лопатки, что позволяет менять параметры турбины в самом широком диапазоне.
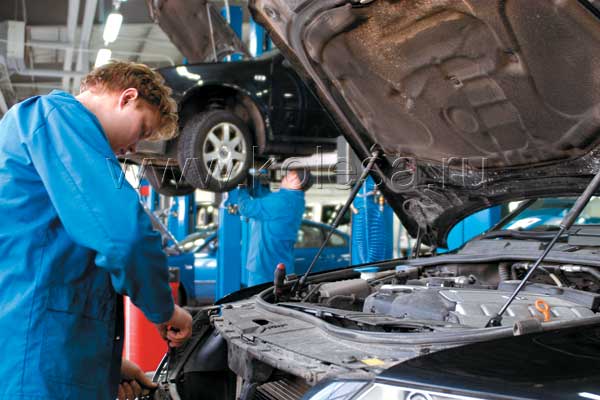
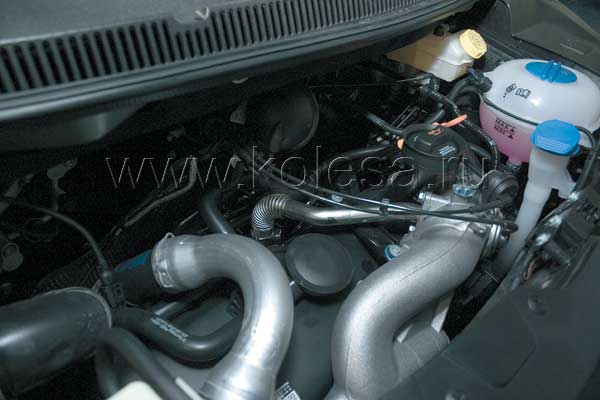
Параллельно с конструкцией для борьбы с инерционностью очень важное значение имеют материалы, из которых изготавливаются компрессоры: турбина должна быть легкой. А также очень прочной: температура выхлопных газов, поступающих на ее колесо, составляет от 650-750 °С у дизеля и может достигать 1 000 °С у бензинового мотора, а частота вращения находится в пределах 4 000-21 000 об/мин. Поэтому колесо турбины отливается в вакууме из жаропрочного никелевого сплава, а корпус – из высокопрочных и высоколегированных марок чугуна. Инновацией сегодняшнего дня стали керамика и полимеры: появляются такие конструкции, как, например, монолитные турбины из спеченого карбида кремния, которые весят в 3 раза меньше обычных при той же механической прочности.
Привереда
Производители закладывают в конструкцию достаточно приличный ресурс, который у современных турбин практически равен ресурсу двигателя. Но только при одном условии – строгом соблюдении всех предписанных норм по периодичности ТО и используемых для обслуживания материалов. Турбокомпрессор – это узел, который практически все время работает в тяжелых условиях и в режиме высоких нагрузок. Поэтому его живучесть оказывается достаточно легко понизить.
Первые враги турбокомпрессора – несвоевременная замена масла или установка некачественного фильтра. В этом случае циркулирующие по масляной системе абразивные частицы (продукты работы двигателя) начинают попадать в подшипниковый узел турбокомпрессора и вызывают его износ. От этого появляется люфт ротора, что, в свою очередь, вызывает износ уплотнительных колец и лопаток колес турбины, и в итоге компрессор выходит из строя. К тому же эффекту и результатам приводит разгерметизация впускного тракта и "подкачка" грязного воздуха мимо фильтра, при которой попадающие извне пыль и песок могут сточить лопатки турбины.
Весьма требователен турбокомпрессор и к четкой работе других систем двигателя – охлаждения и прокачки масла. Особо чувствительным местом на практике оказывается подшипниковый узел турбокомпрессора, поскольку масло, поступающее в него, кроме непосредственно смазывания также выполняет функции охлаждения и демпфирования ротора, гася его колебания. В случае же ухудшения прокачки масла подшипники компрессора начинают интенсивно изнашиваться – и скоро станет необходимым ремонт.
Для турбокомпрессоров весьма характерен эффект "снежного кома", когда малейшая неисправность и даже небольшое нарушение параметров работы в одном месте неизбежно ведут к появлению связанных с узлом других неисправностей и, в итоге, к поломке агрегата. И при этом падение мощности двигателя, повышенный расход масла в моторе, появление масляных потеков на патрубках впускного и выпускного трубопроводов, вдруг появившийся посторонний звук, черный или синий окрас дыма из выхлопной трубы – все это может быть "симптомами начала болезни". Обнаружив их, в сервис ехать нужно не откладывая.
Впрочем, заметим, что у машин, купленных новыми в автосалоне и обслуживаемых по гарантии в дилерском сервисе, проблем с турбонаддувом в подавляющем большинстве случаев не возникает. Регулярные ТО по технологии производителя машины и применение сертифицированных материалов (масел, фильтров и т.д.) обеспечивают турбокомпрессору надежность и безотказность. Но вот при покупке "сэконд-хенда", особенно того, что успел поездить после ремонта, могут быть проблемы: неизвестно как эксплуатировал и обслуживал свой автомобиль прежний владелец. Поэтому после первичного осмотра непременно стоит заехать на диагностику в автосервис – за ремонт турбокомпрессора меньше чем $500-700 заплатить не получится.
Для комментирования вам необходимо авторизоваться